Tap – Feeds and Speeds
America´s Finest High–Speed Cutting Tools™
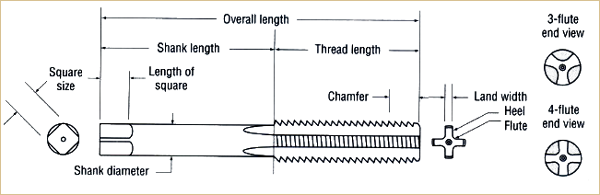
How to Tap Effectively and Optimize Tool Life To minimize tapping issues the following rules should be followed:
-
• Use a pitch controlled tapping attachment.
• Choose the correct lubricant (Ultra S/P™ Super Premium).
• Use the correct Tapping Drill Size and Type of Tap.
• Choose the correct Speeds and Feeds.
• Keeping taps sharp, check tap for wear.
• Ensure accurate alignment.
• Check hardness of material, especially when changing batches of material.
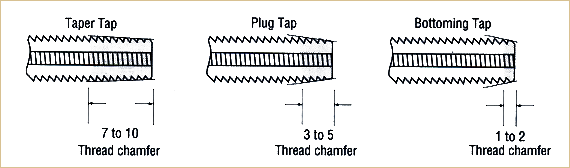
Tapping Speed can be calculated using: (Use Table below)
RPM = Feed Speed (SFM) / 0.26 x Tap's Outer Dimension
Tapping speeds should be "DECREASED" if
-
• Lubricant is Poor, or Flow is Restricted.
• Bottom lead or Spiral flute taps are used.
• Thread depth ( % ) increase.
• Thread pitch is course.
• Cutting taper threads (50% Normal Speed).
-
• Thread Depth decreases.
• Thread Pitch is fine.
• Coolant flow and Quality is Good.
• Spiral point taps are used.
Recommended Feeds and Speeds table below suggests a "starting point" for selecting the speed to operate the tap.
Material | Recommended Starting Point Feeds and Speeds(SFM) |
Aluminum - Cast Alloys | 60 |
Aluminum - Diecast Alloys | 70 |
Aluminum - Wrought Alloys | 80 |
Brass | 60-100 |
Bronze | 30-40 |
Copper | 60-80 |
Gun Metal | 50-60 |
Cast Iron - Grey | 30-60 |
Cast Iron - Ductile | 50 |
Cast Iron - Alloys | 15-30 |
Malleable Alloy | 20-40 |
Magnesium Alloys | 50-70 |
Nickel Alloys | 10 |
Nimonic Alloys | 10-12 |
Mild Steel | 30-50 |
Steel - Medium Carbon | 35 |
Tool Steels | 15-25 |
Cast Steel | 25 |
Titanium Alloys | 10 |
Stainless Steel - 300 Series | 10-20 |
Stainless Steel - 400 Series | 15 |
Plastic | 50-70 |
Zinc - Diecasting | 80 |